
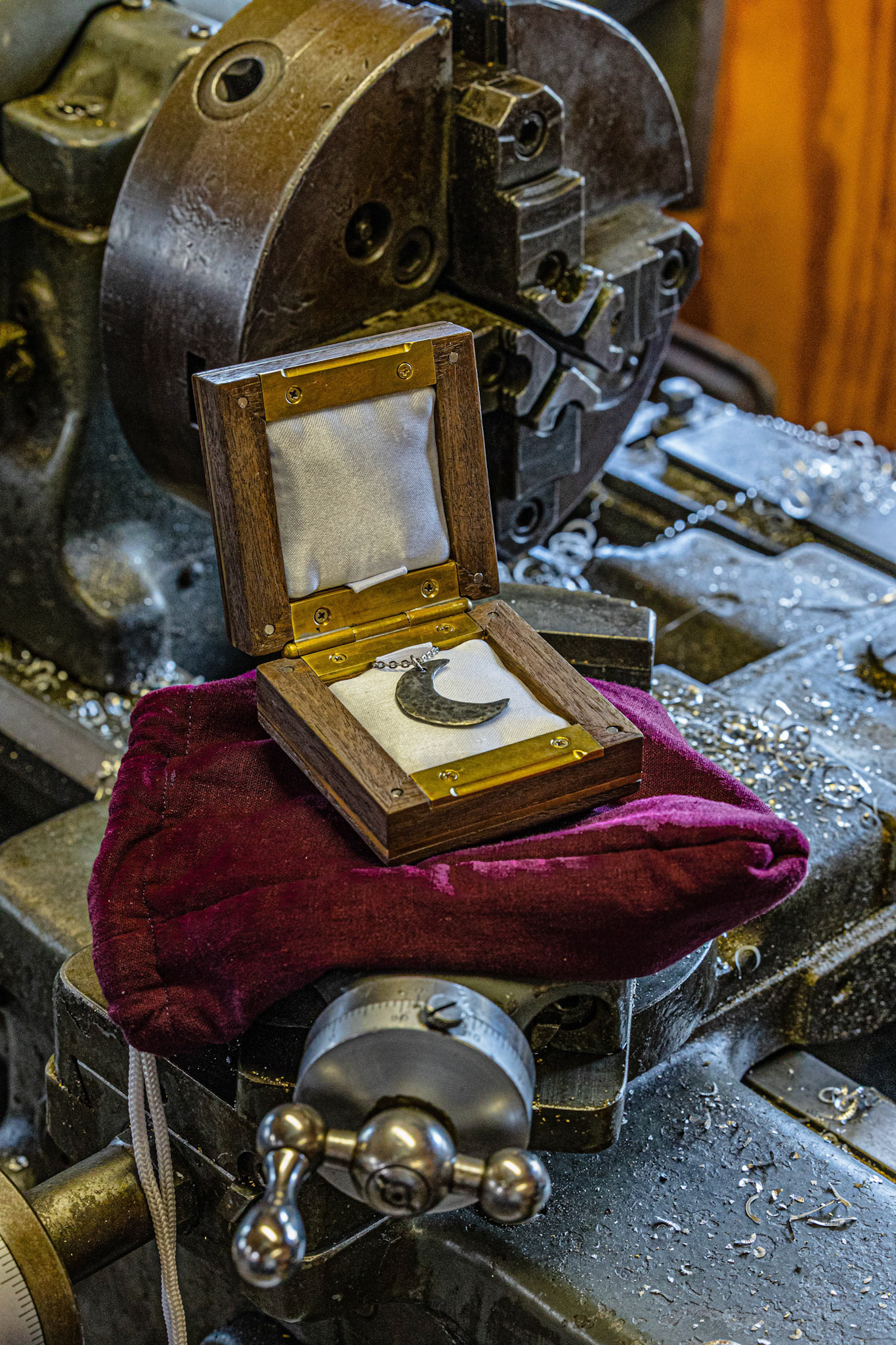
Thomas Johnson '22, Box
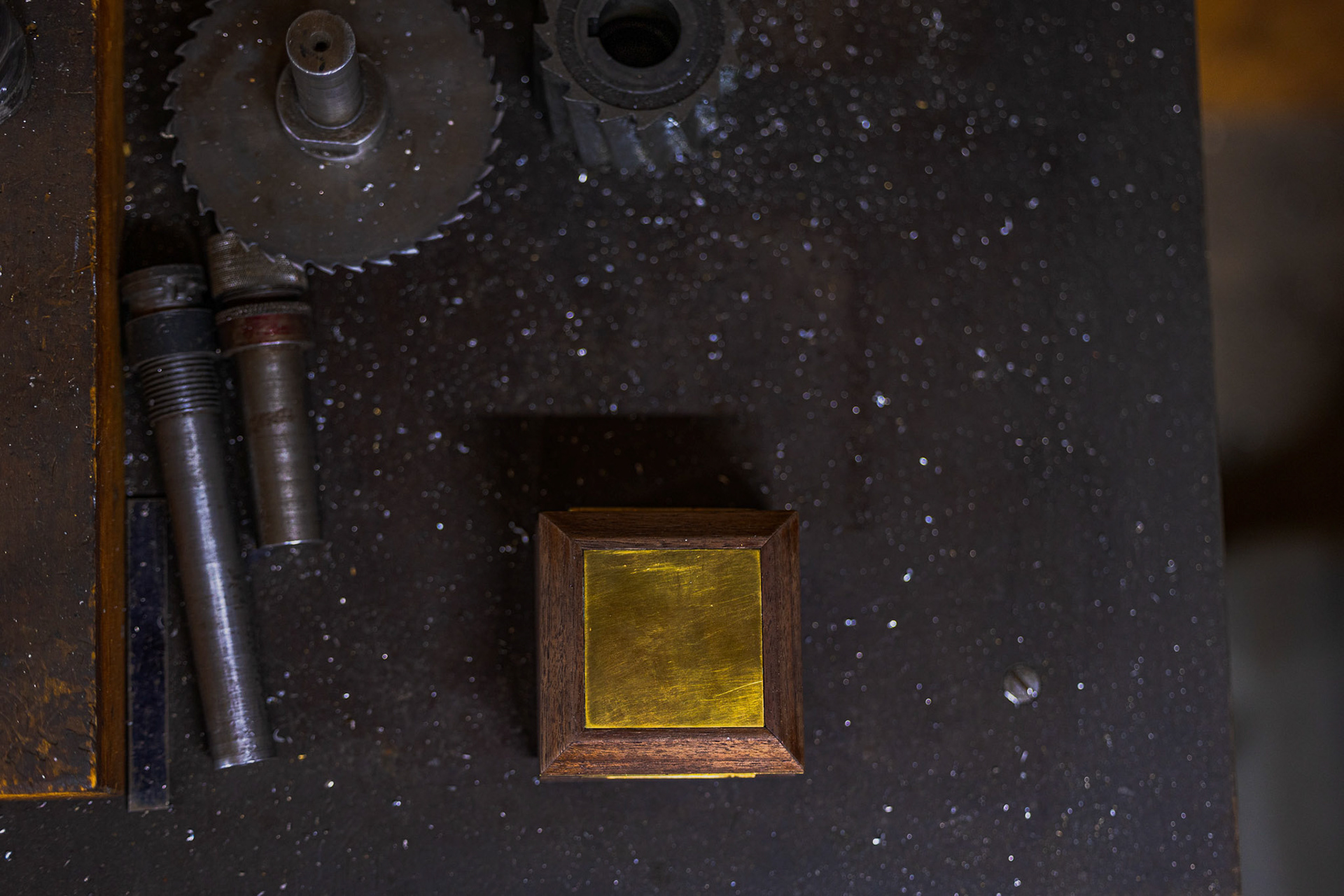
Thomas Johnson '22, Box
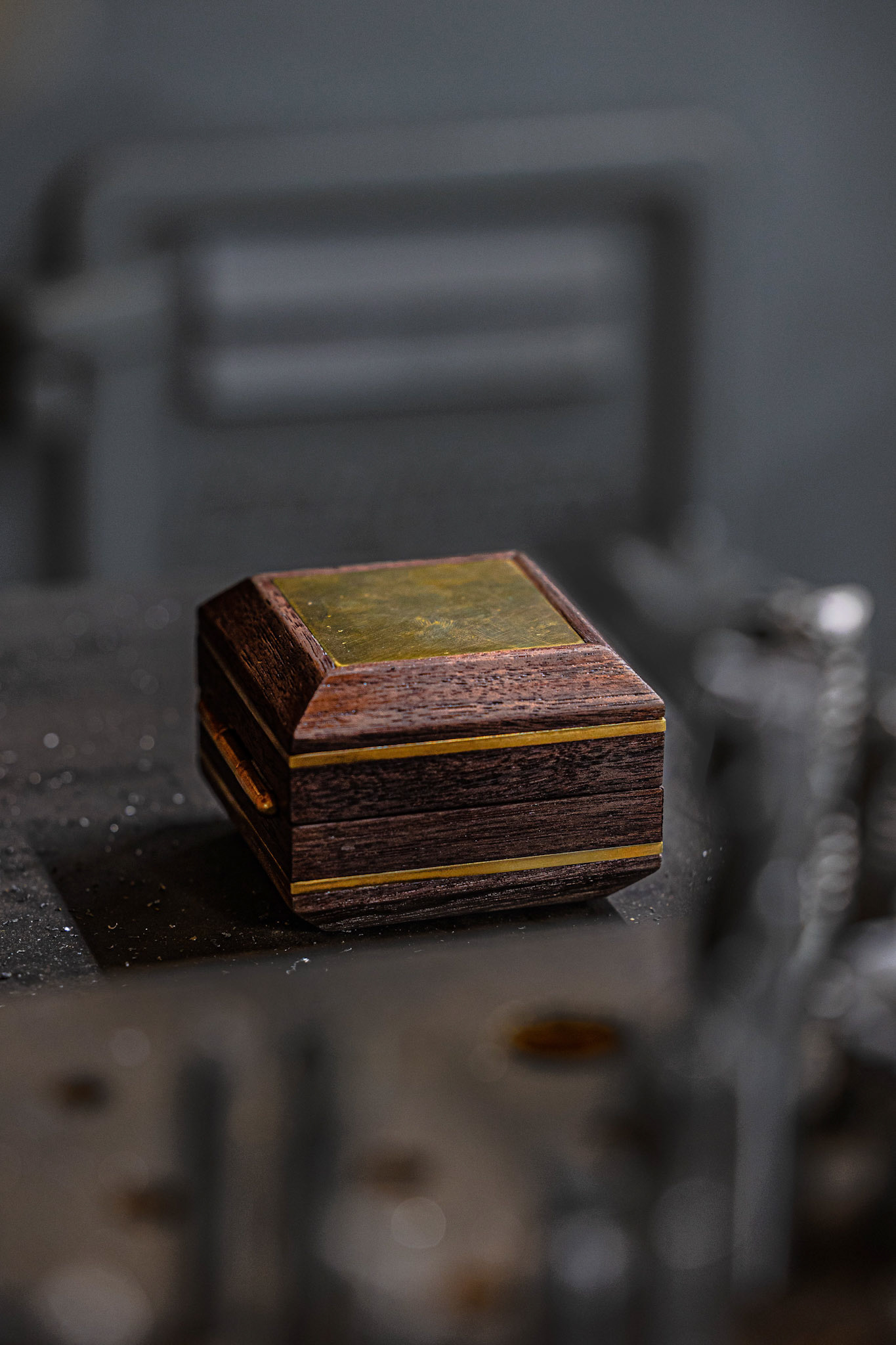
Thomas Johnson '22, Box
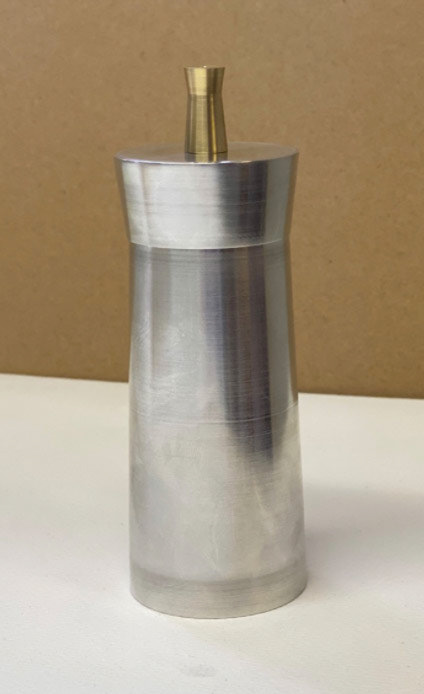
Ella Makechnie ‘23, Pepper Grinder
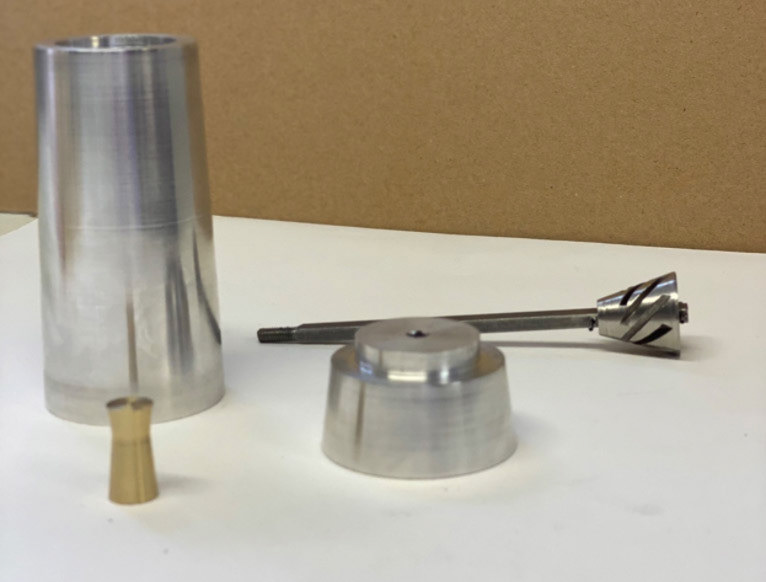
Ella Makechnie ‘23, Pepper Grinder
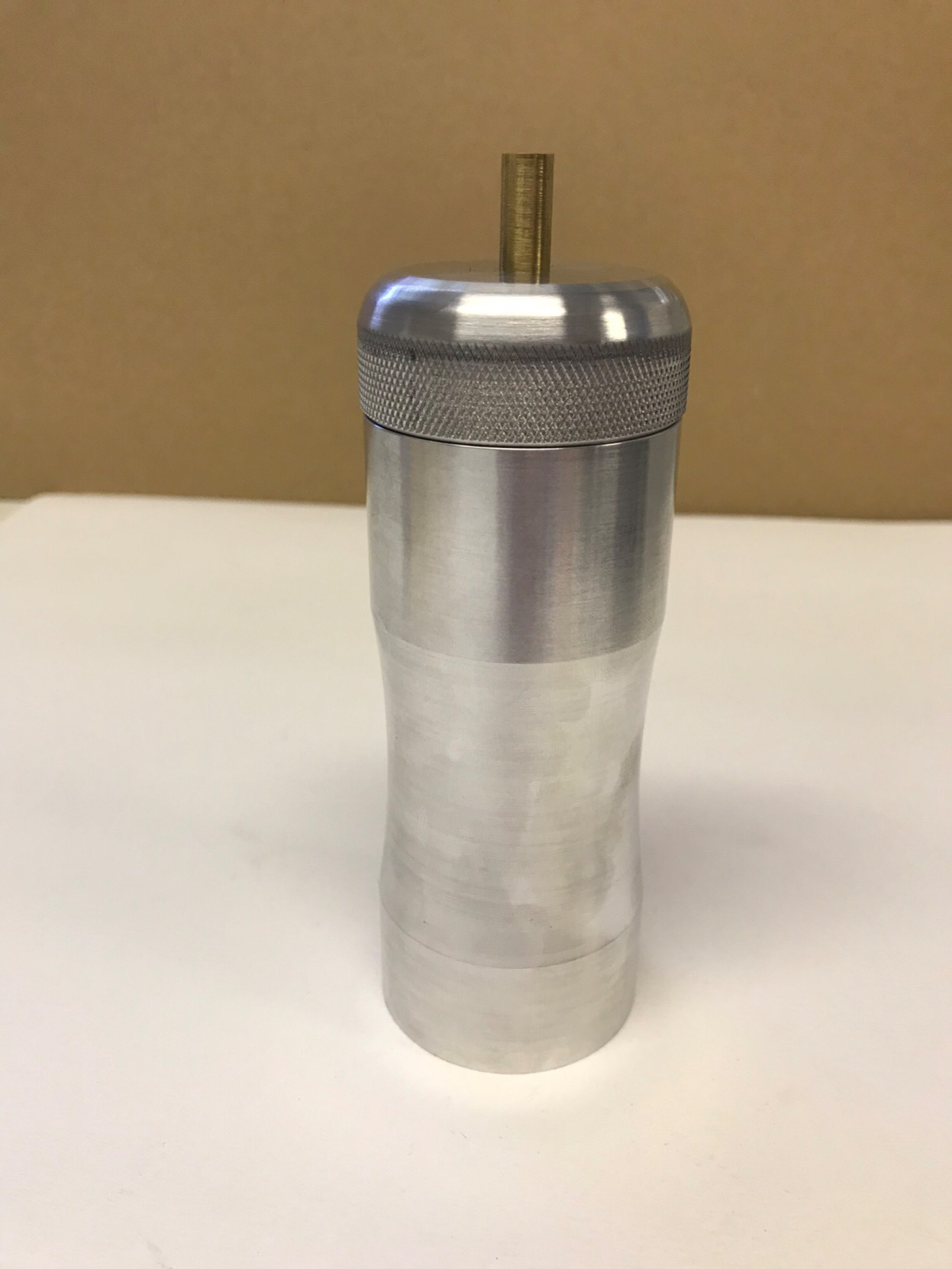
Ada Gardner ‘22, Pepper Grinder
Metal engineering was a new area for me. Not only had I never used any of the tools but designing and engineering a functional piece was a learning experience. My pepper grinder started out on paper as a rough sketch of my ideal design. From there I learned how to precisely create the inner workings of the tool so that in the end it would successfully grind pepper. Once the working parts were done, I transferred my rough ideas into a measured mechanical drawing. From here I had the information to create the final product. Throughout the whole process I learned how to operate the machines to do a variety of different cuts and finishes. Some of the more artistic features of my pepper grinder were equivalently artistic in term of how they were accomplished on the machines (ie. C-clamping a piece of metal to the lathe to make a jig, so that I had more control for a sweeping curve). Overall, metal engineering combined aspects of precision and art in a medium that I had never explored before while creating a usable pepper grinder.
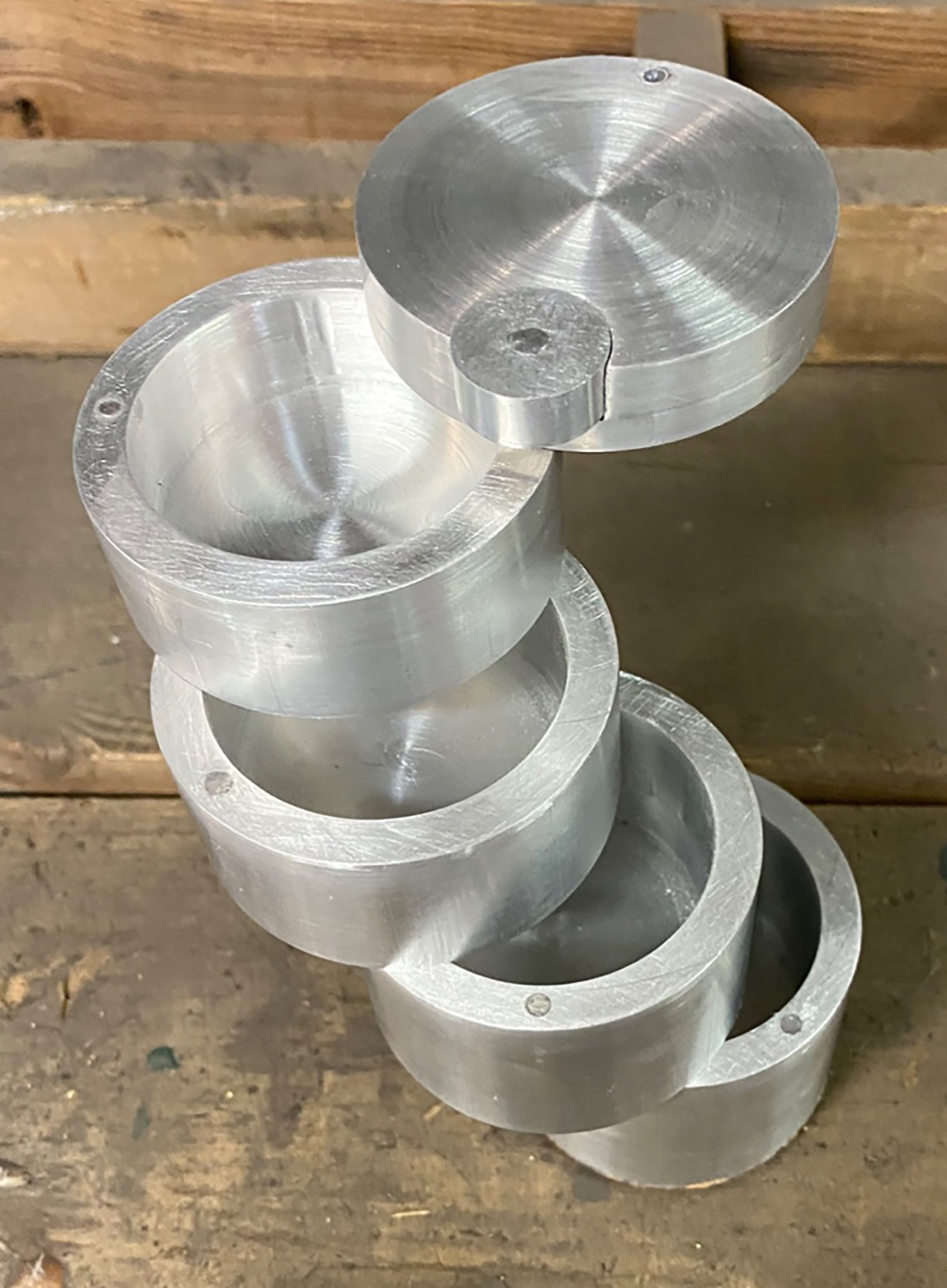
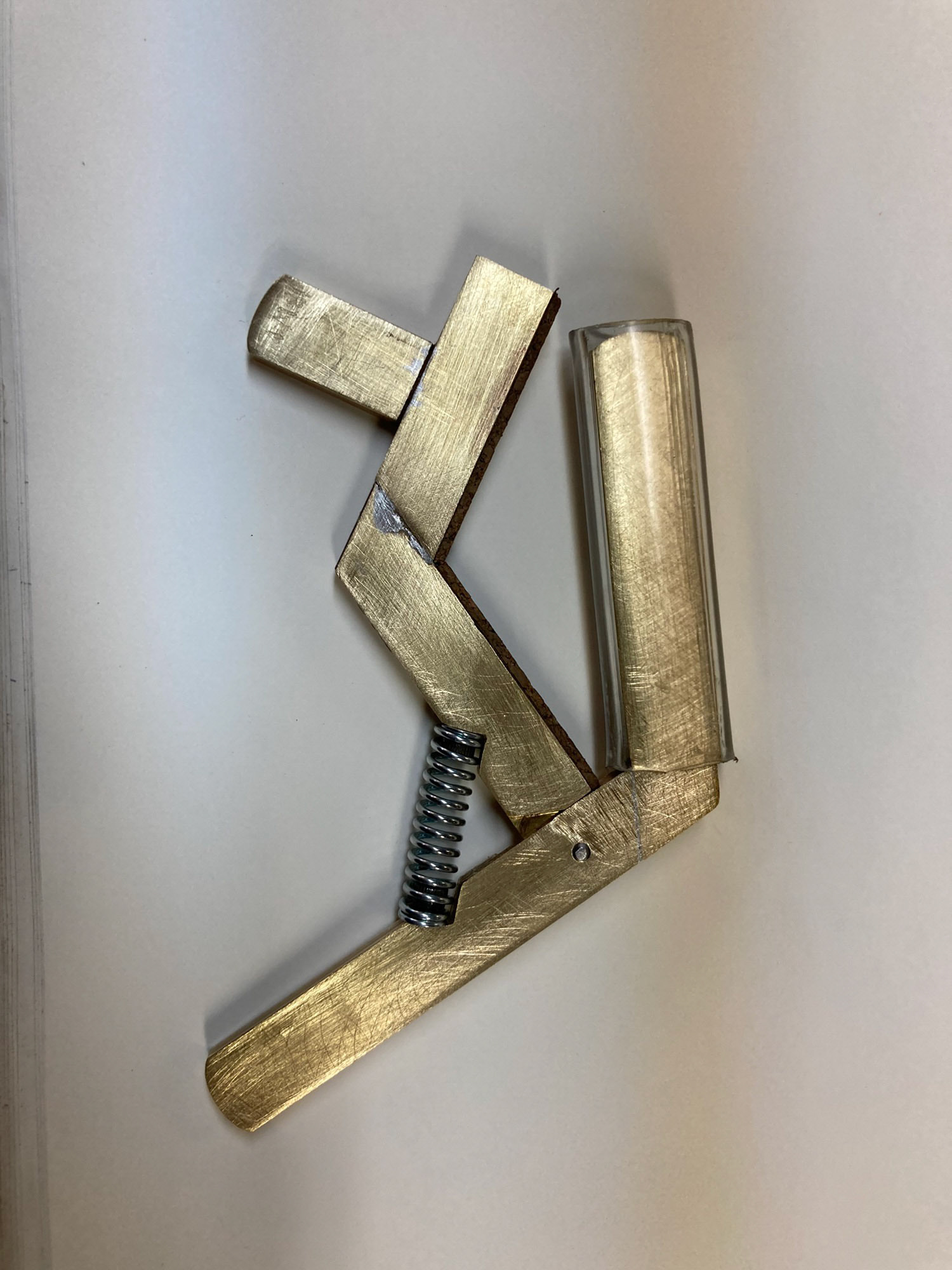
Jules Warmke '21, Guitar Capo
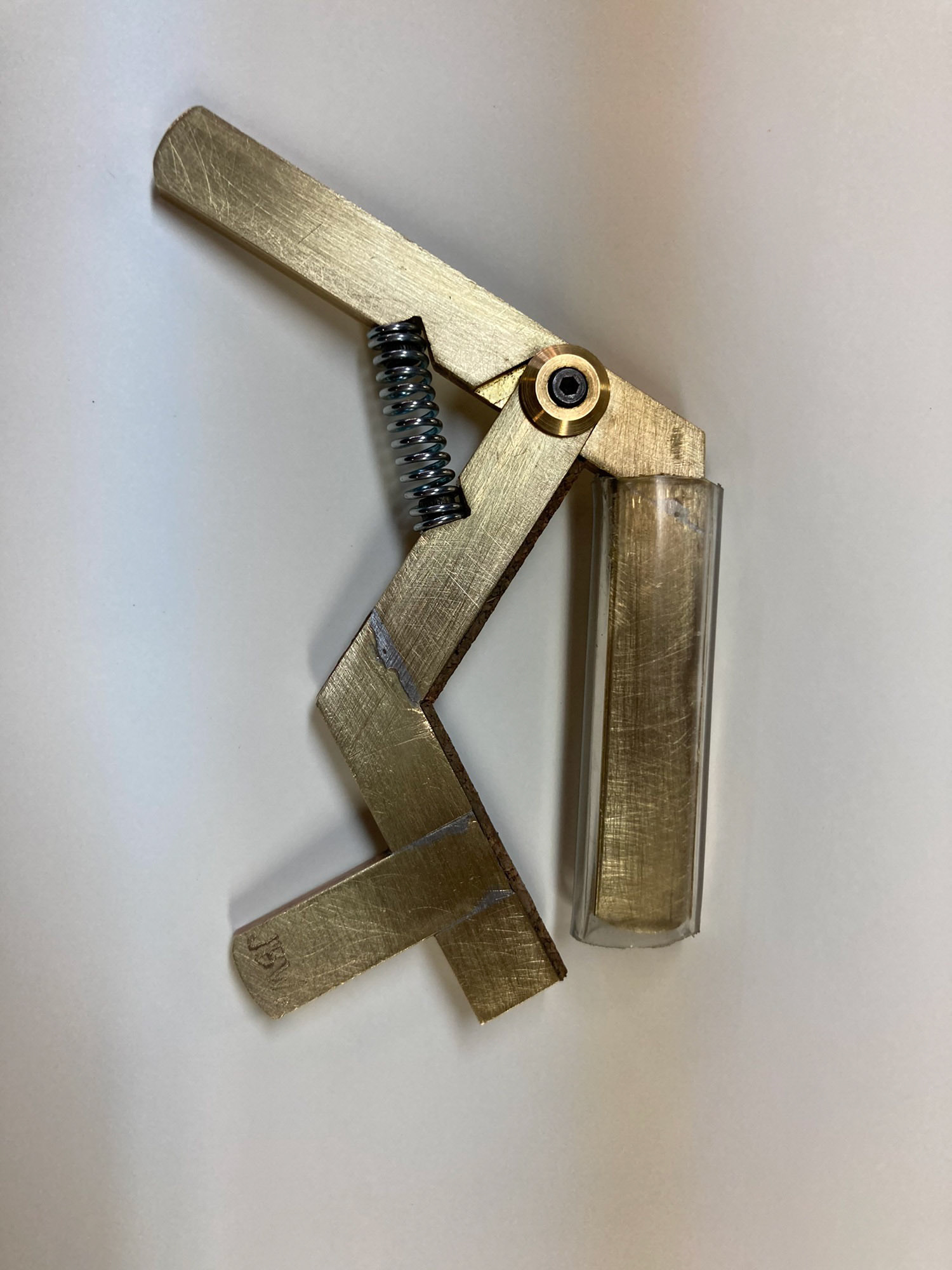
Jules Warmke '21, Guitar Capo
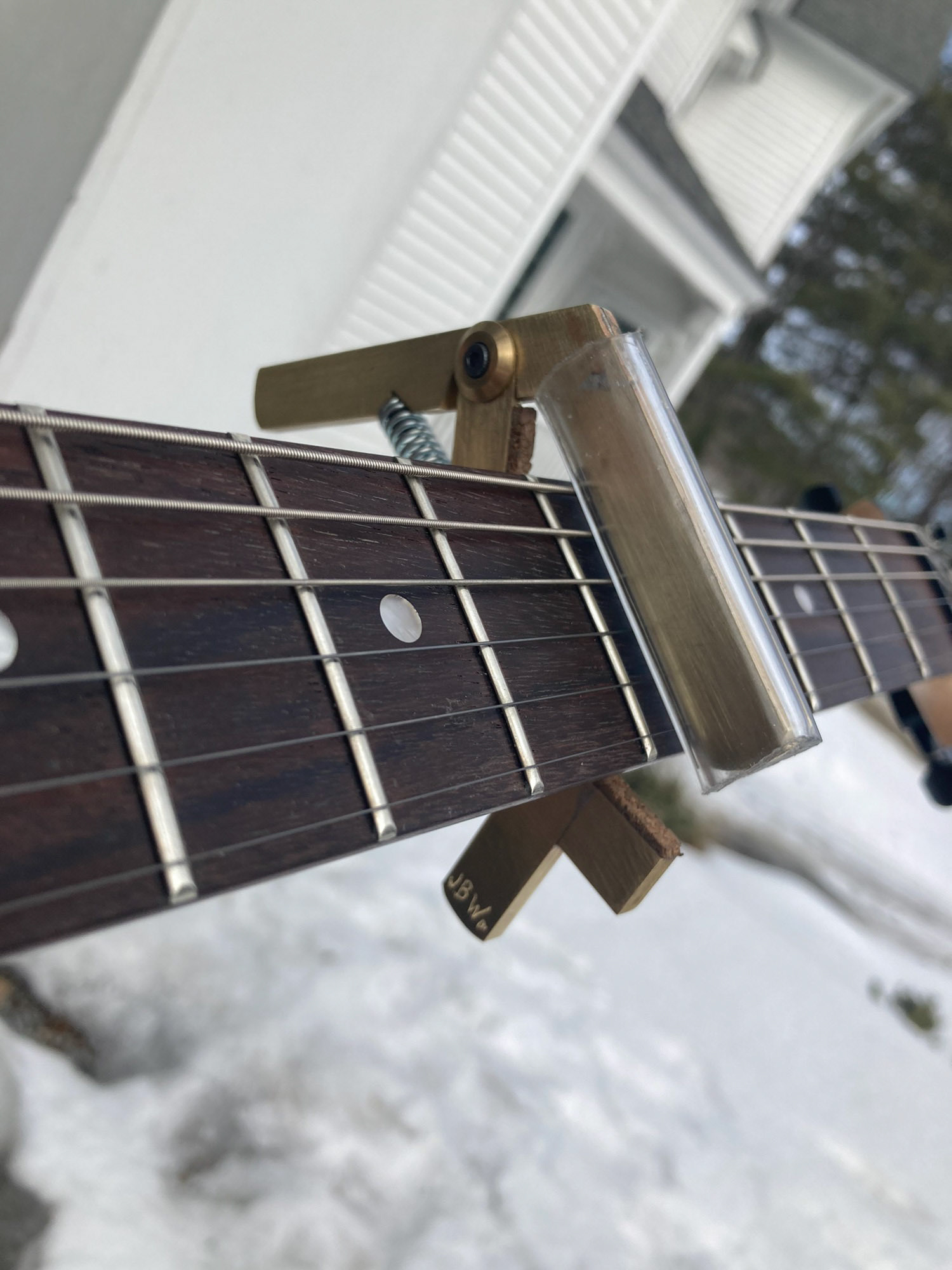
Jules Warmke '21, Guitar Capo
Cole Doolittle '24, Pepper Grinder
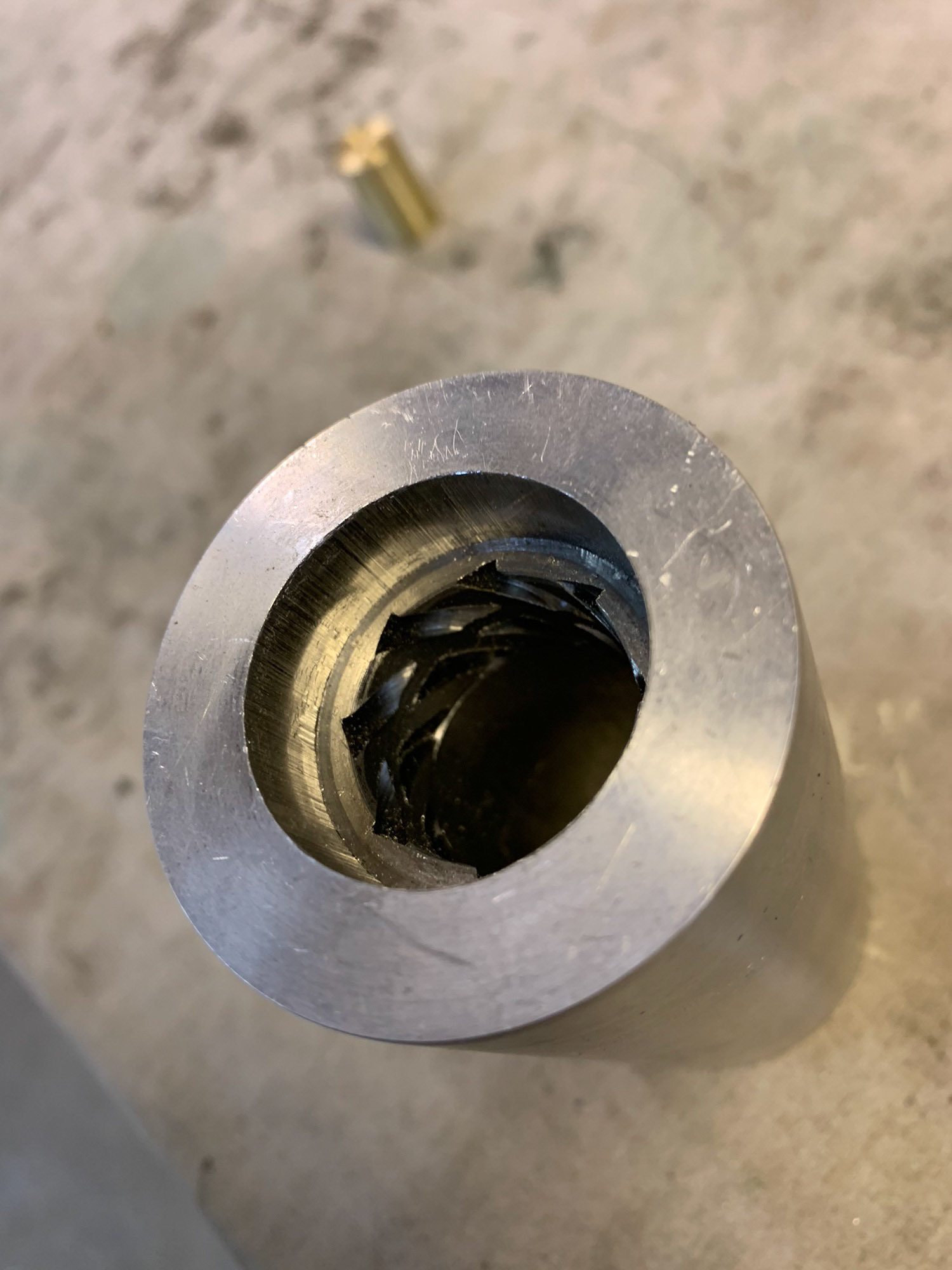
Henry Krehbiel ‘23, Pepper Grinder

Henry Krehbiel ‘23, Pepper Grinder

Henry Krehbiel ‘23, Pepper Grinder
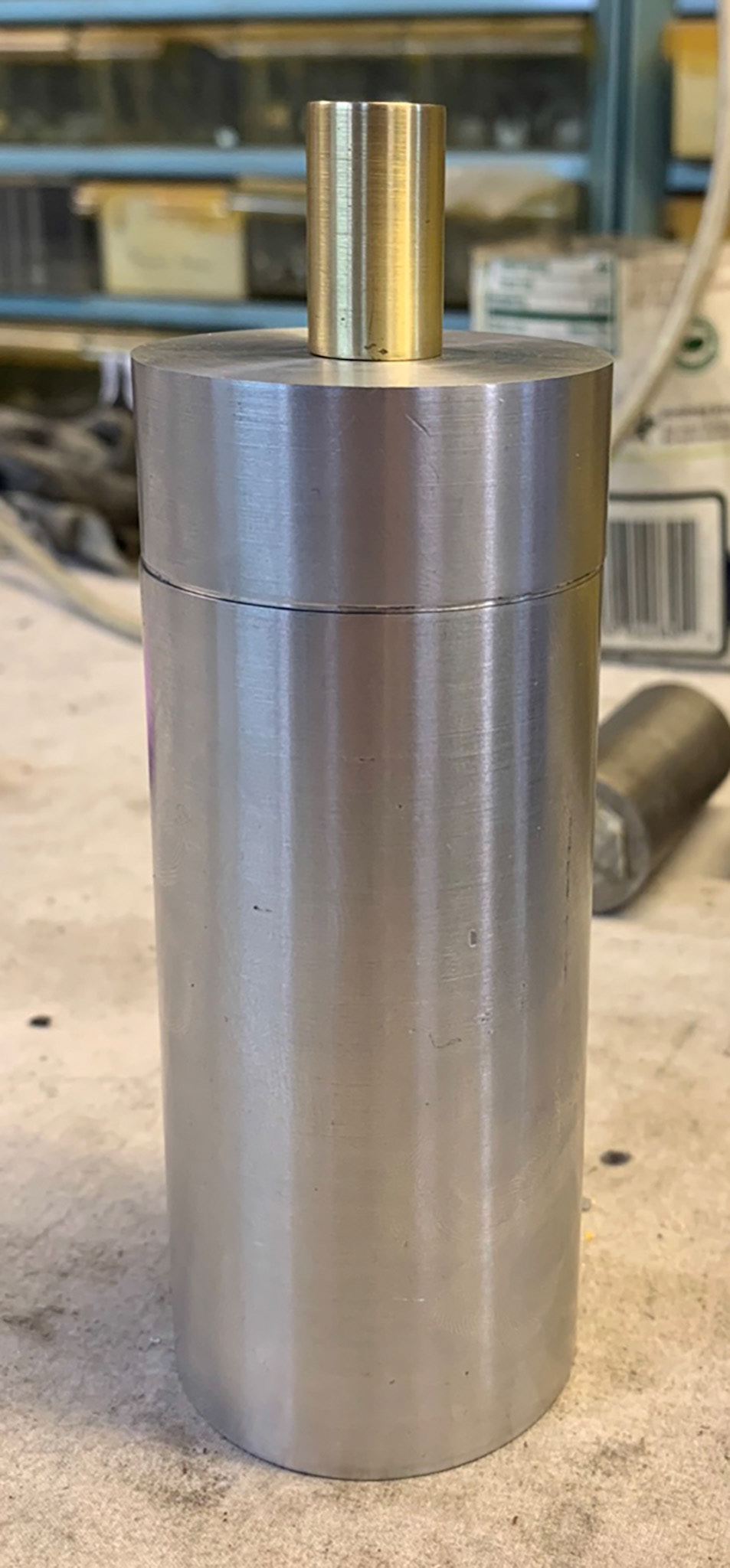
Henry Krehbiel ‘23, Pepper Grinder
Jackson Gramache '24, Pepper Grinder
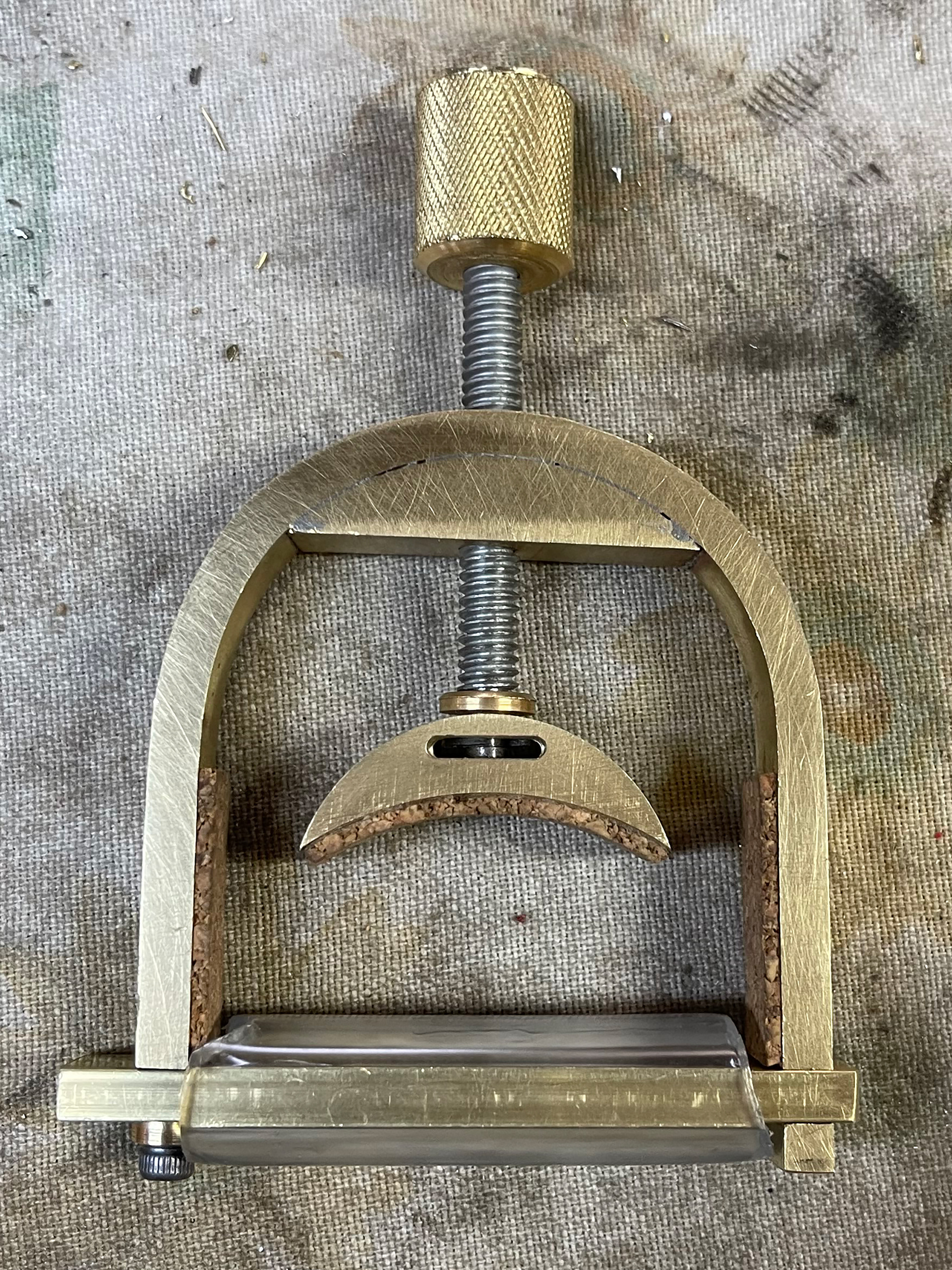
Mason Guerster '22, Guitar Capo

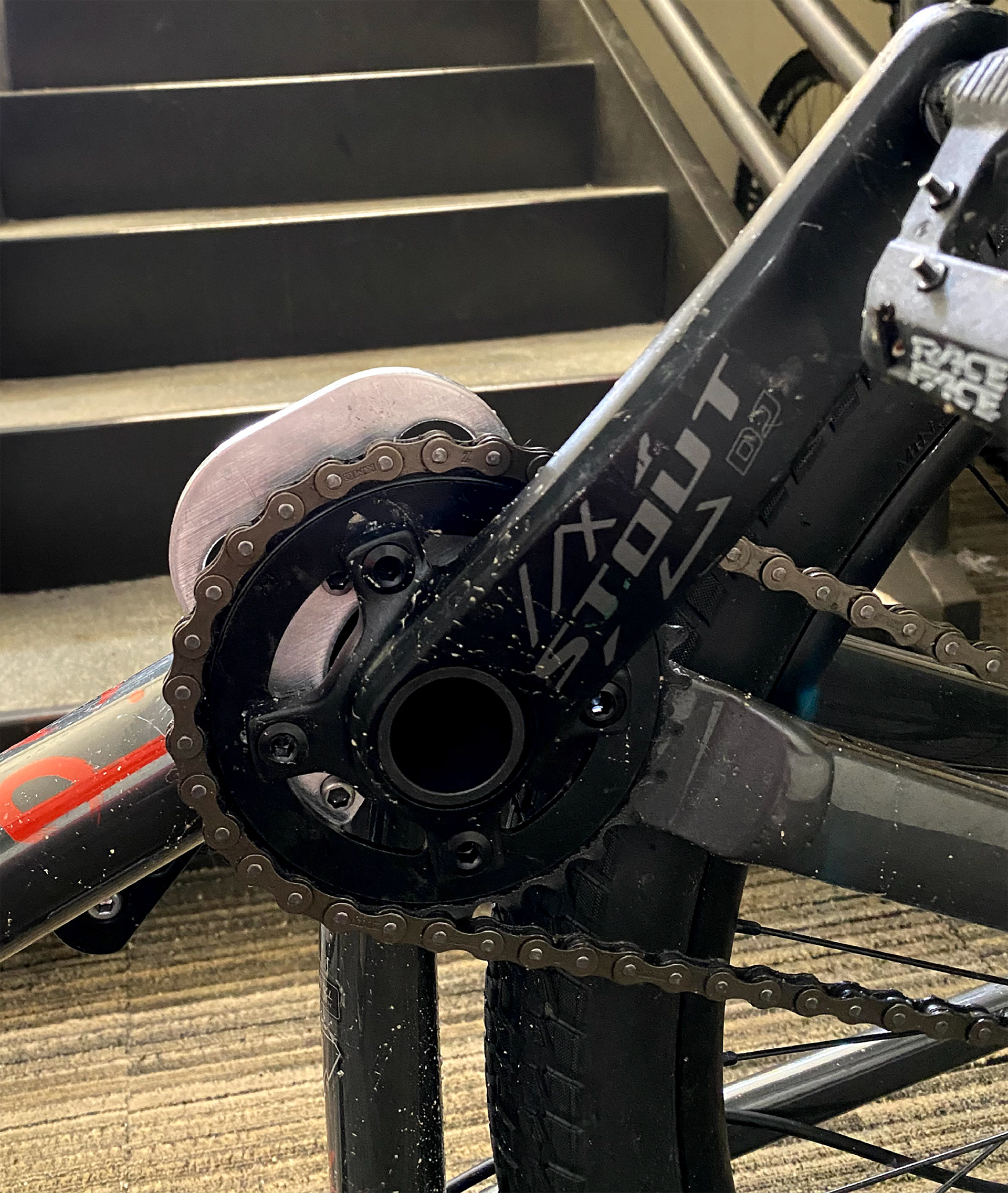

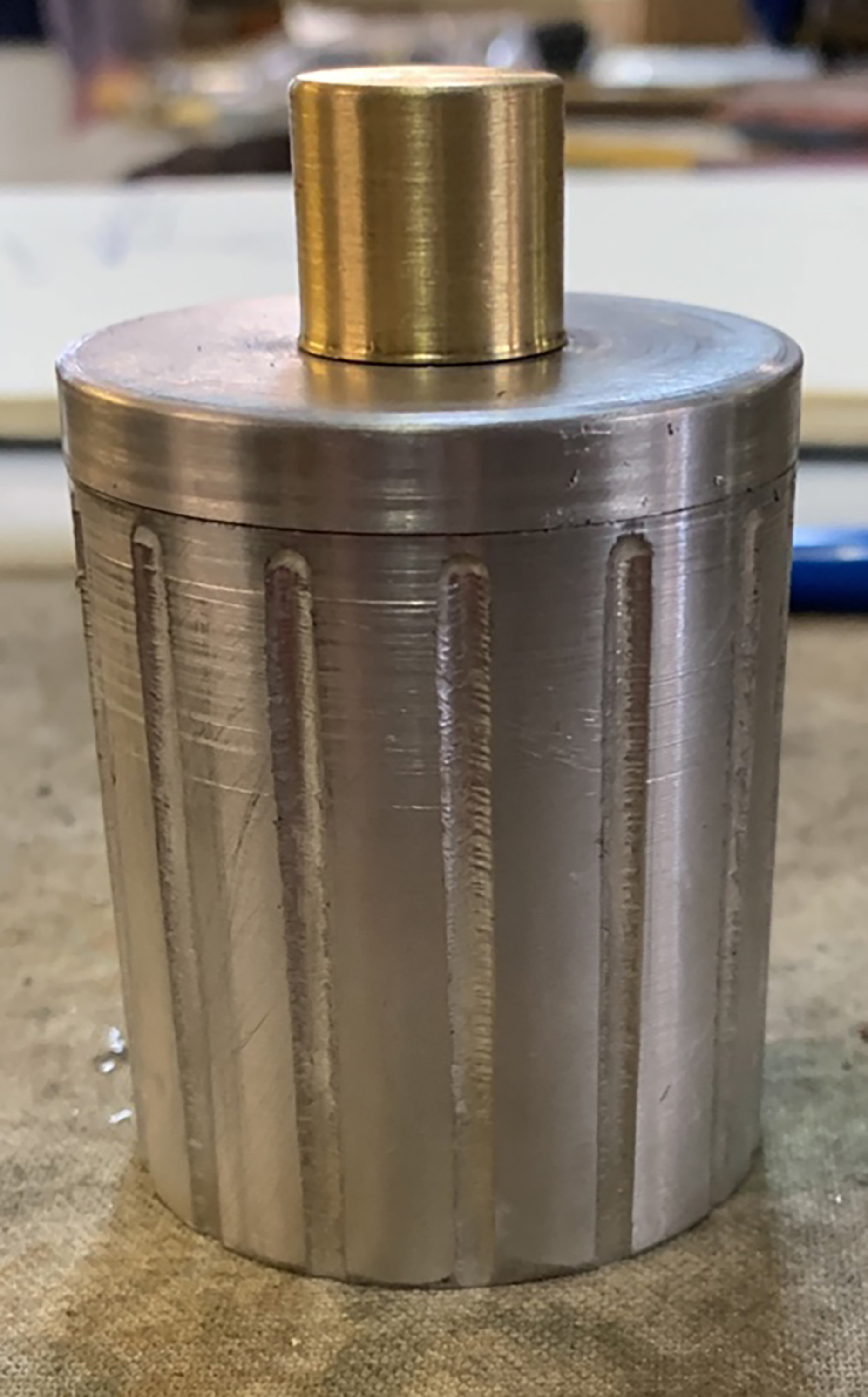
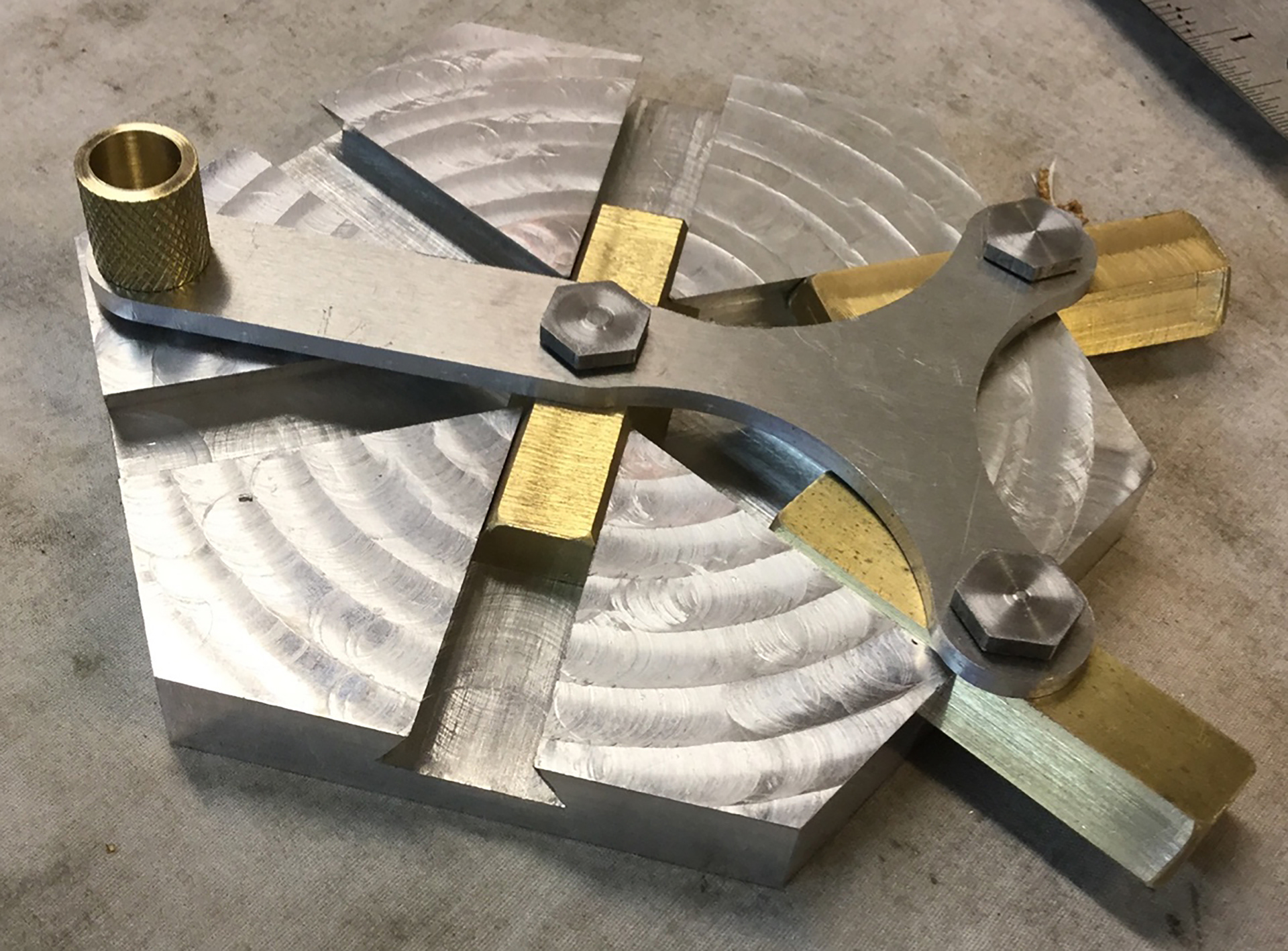
Ezra Taylor '21

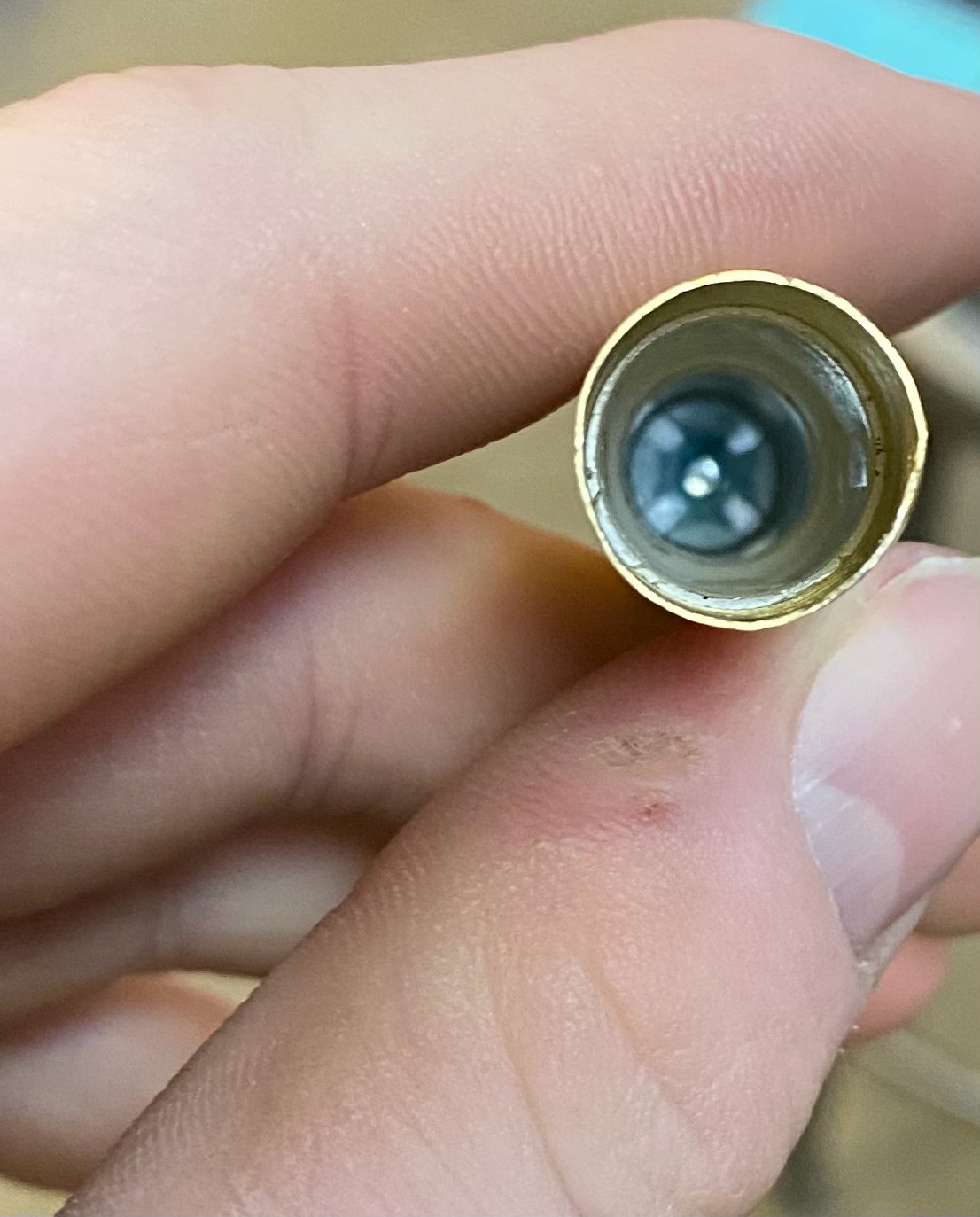
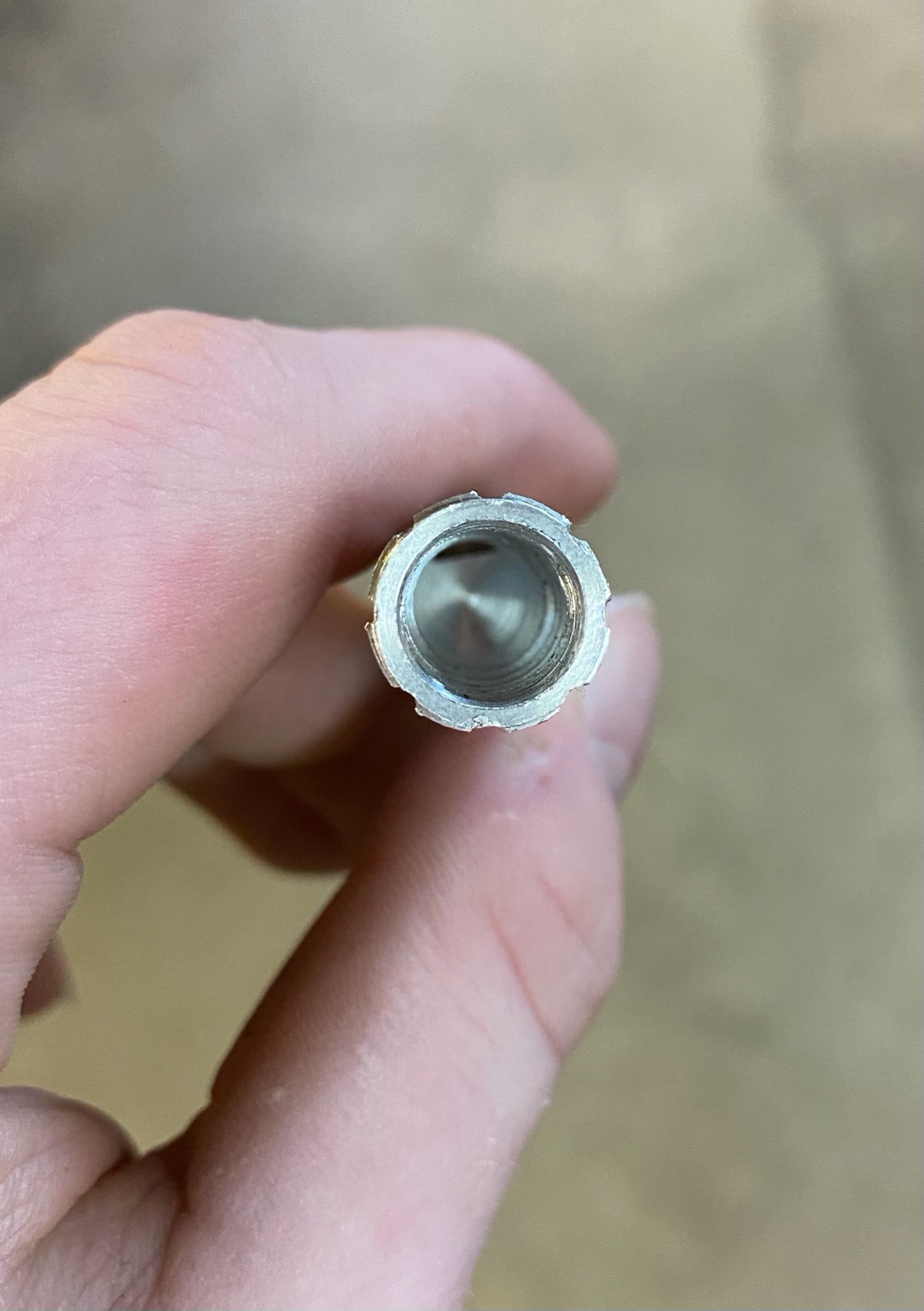
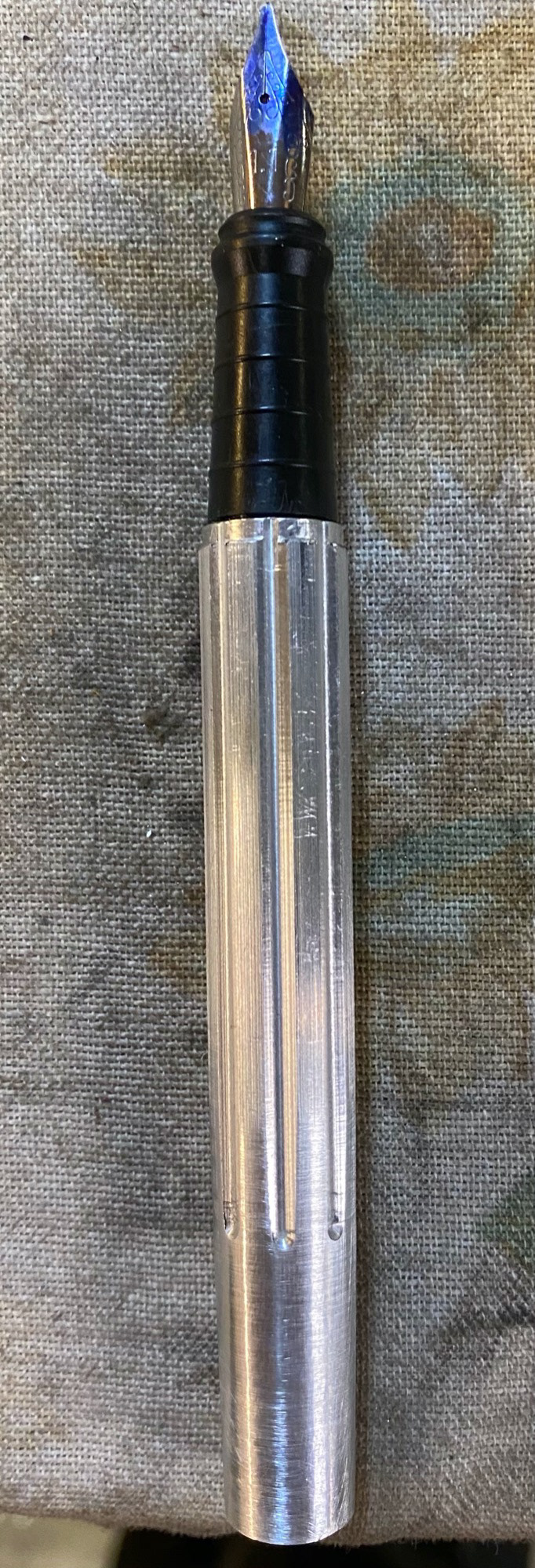
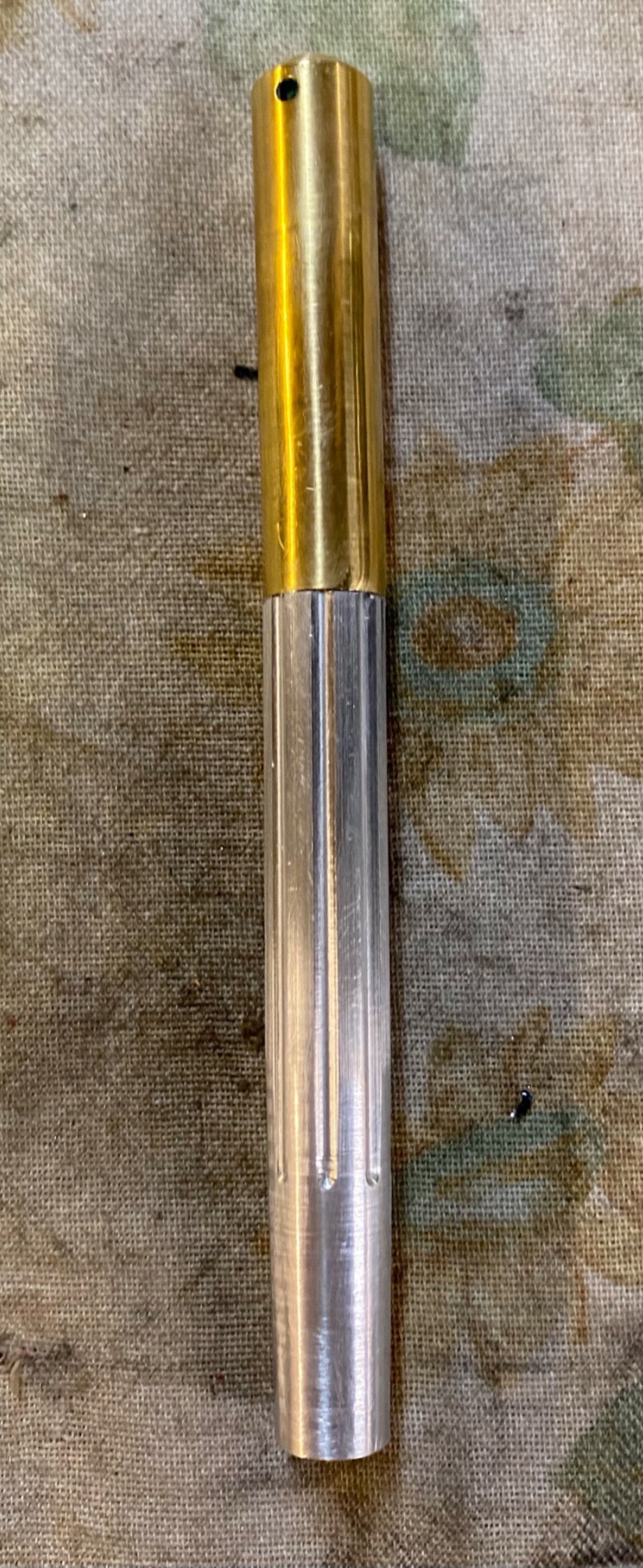